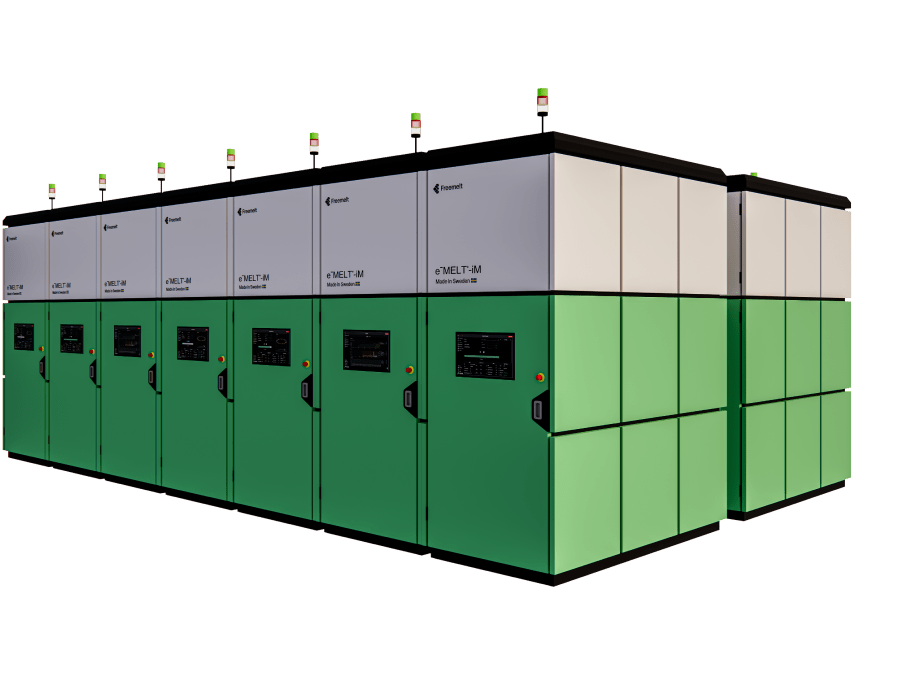
Elevating tungsten manufacturing-Six reasons to choose e¯MELT®
Introduction
Tungsten has several exceptional properties that make it highly valuable for industrial use. Tungsten is a refractory metal, and has the highest melting point among all elements, at 3,422°C, which makes it extra resistant to heat. Traditional manufacturing of tungsten components is challenging and costly, especially when aiming for the highest material properties. Additive Manufacturing (AM) and E-PBF (Electron Beam Powder Bed Fusion) offer promising solutions to these challenges. AM enables the production of tungsten components with complex geometries that are difficult or impossible to achieve with traditional methods. Additionally, AM can reduce material waste, shorten production times, and allow for more flexible manufacturing processes.
This advancement has increased the interest in tungsten across various industries, including medical X-ray equipment, rocket engine components, defense ammunition, and components for fusion energy power plants.
Freemelt’s e–MELT® machine is designed for serial production, and with its unique features, it is an optimal choice for tungsten manufacturing.
1. Diode electron gun for stable beam quality
e–MELT® is built on a grid-less electron gun based on a diode design. Unlike the triode electron guns used in other E-PBF systems, which degrade in quality at higher beam power, the e–MELT® ’s diode gun maintains a stable beam spot size throughout the full power range (0 to 6 kW). This consistency is crucial for tungsten processing because a high beam power is a great advantage for reaching high productivity in this process that requires a powder bed temperature above 1200 °C.
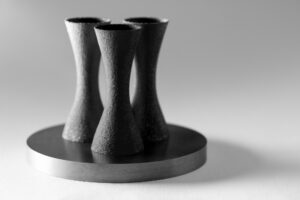
Image 1. Tungsten nozzles built in a Freemelt machine
2. Active water cooling for enhanced productivity
Freemelt’s e–MELT® machines stand out as the first in the E-PBF market to offer active water cooling during and after the build. Continuous cooling during the build allows the use of higher melt power and speeds without overheating the powder bed. The water cooling also drastically reduces the post-cooling time. For tungsten, with its high thermal conductivity, this feature is particularly beneficial, cutting post-cooling times to as low as 30 minutes from the usual several hours.
3. Dockable build module for minimal dead time
Productivity is further enhanced by e–MELT®’s dockable build module system. Each module is a self-contained unit that includes both the build tank and the powder feeding system. With dual modules, one is used for production while the other module is prepared for the next build in a standalone turnaround station. This feature significantly minimizes machine downtime between builds and increases overall productivity.
Image 2. The docking system illustrated in e–MELT®-iD
4. Superior vacuum quality for clean processing
Tungsten’s sensitivity to oxygen makes a controlled environment essential. Tungsten contaminated by oxygen is prone to cracking. e¯MELT® features the smallest vacuum chamber in the market, with dual turbomolecular pumps that achieve a vacuum as low as 10-5 mbar. This ultra-clean environment prevents oxygen contamination and even purifies tungsten during processing, achieving oxygen levels as low as single ppm, which is critical for superior material quality.
5. Spot melting for stress reduction and microstructure tailoring
Freemelt’s innovative spot melting technique, supported by the Pixelmelt® software, offers significant advantages over traditional line melting. By rapidly creating submillimeter melt pools, spot melting evenly distributes heat, reducing residual stress and the risk of macroscopic swelling. Moreover, the ability to customize spot melting patterns allows for site-specific microstructure tailoring, a promising development for future E-PBF applications.
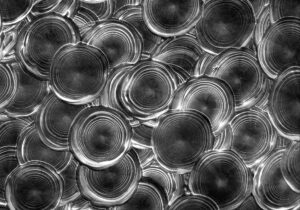
Image 3. Quasi-random Pixelmelt® pattern of melt pools on the top surface of E-PBF tungsten. Image from a build in a Freemelt machine
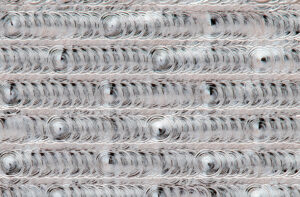
Image 4. Ordered Pixelmelt® pattern of melt pools on the top surface of E-PBF tungsten. Image from a build in a Freemelt machine
6. In-situ process monitoring for quality assurance
Finally, e–MELT® machines incorporate in-situ process monitoring through electron imaging. Tungsten’s high electron emission enables high-contrast, detailed imaging, providing real-time feedback on the build’s internal structure. This is particularly valuable for tungsten, which is difficult to inspect using conventional non-destructive methods like X-ray tomography. With this capability, manufacturers can detect and address defects during the build, ensuring the highest quality in the final parts.
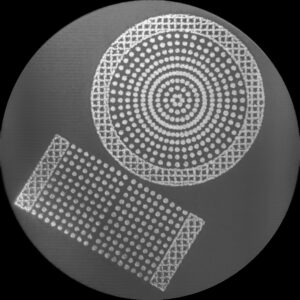
Image 5. Layer image from an arbitrary tungsten build, recorded with the electron detector in a Freemelt machine
Summary
Freemelt’s e–MELT® machine transforms tungsten manufacturing by overcoming challenges associated with traditional methods as well as competing additive manufacturing methods. Its advanced E-PBF technology enables the production of complex tungsten parts with reduced waste and faster production. Key features include a stable diode electron gun, active water cooling for efficiency, dockable build modules for minimal downtime, superior vacuum quality to prevent contamination, spot melting for stress reduction, and in-situ process monitoring for quality assurance. With these innovations, e–MELT® sets a new standard for productivity and material quality in tungsten manufacturing, supporting applications ranging from defense to energy and medical technology.
Read more
Freemelt material strategy
Electron beam powder bed fusion processing of pure tungsten
Metal AM Magazine – Mastering tungsten manufacturing with BPF-EB Additive manufacturing