Industrial 3D printer setting the industry standard for serial production
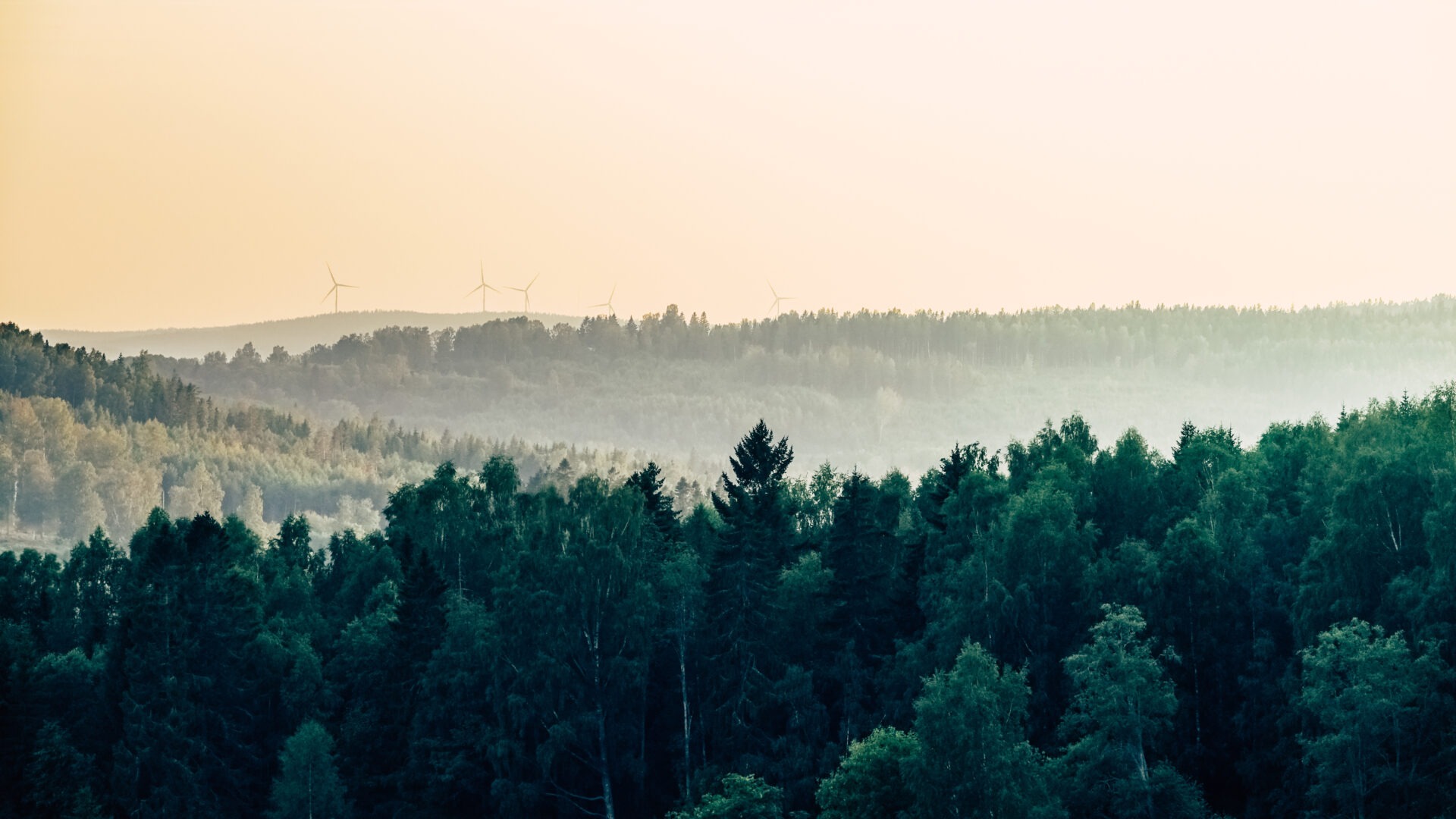
Transform manufacturing
— for good
Freemelt develops advanced 3D printers for metal components, aiming to become the leading supplier in additive manufacturing (AM) by leveraging our E-PBF (Electron Beam Powder Bed Fusion) technology. By positioning ourselves as a productivity partner we support our customers throughout the entire development journey, from feasibility studies to full-scale production. Our solutions primarily serve companies in the defense, energy, and medical technology sectors in Europe and the U.S., enabling them to innovate and enhance production efficiency.
Freemelt’s modular printers, designed for industrial applications, support complex geometries and high-performance materials, such as tungsten for defense and energy applications and titanium for medical implants

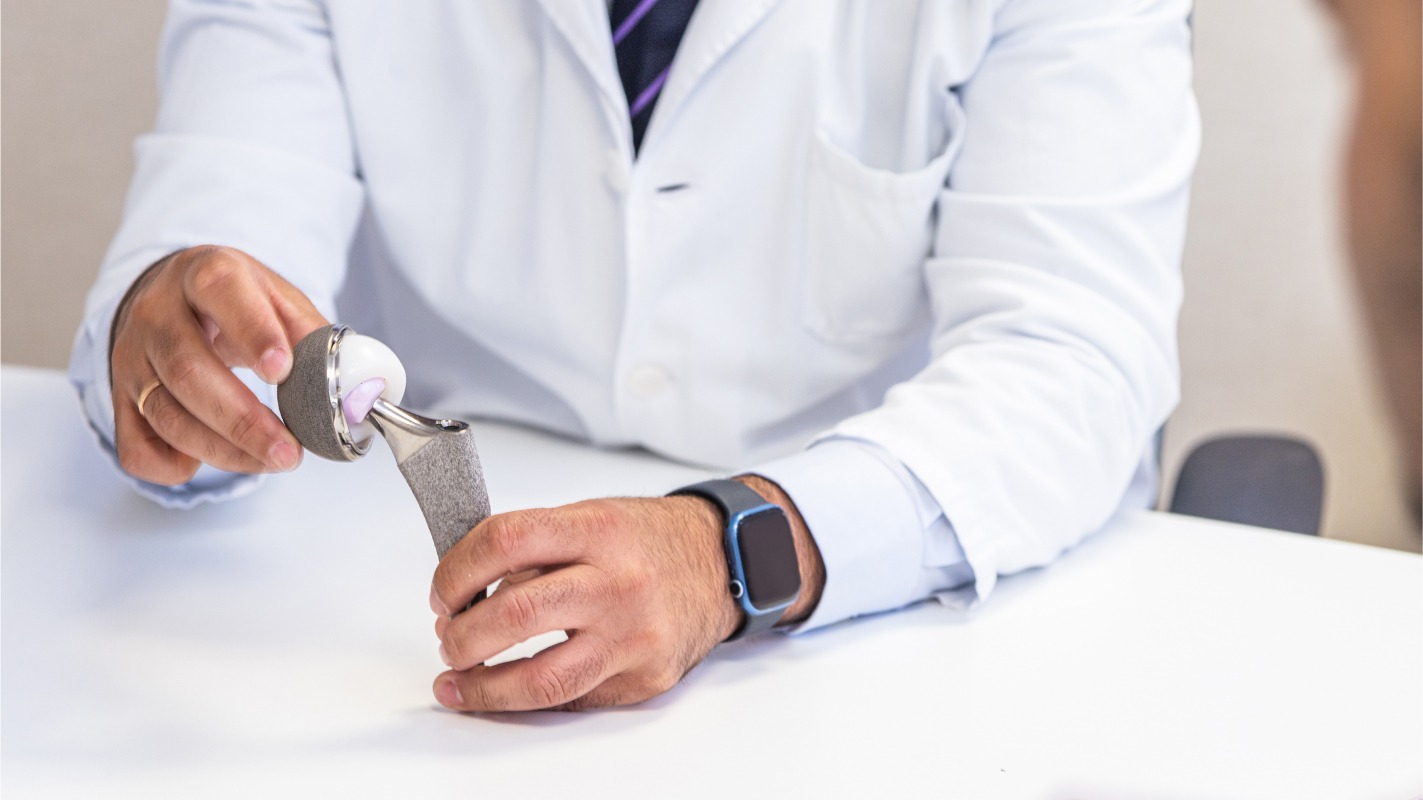
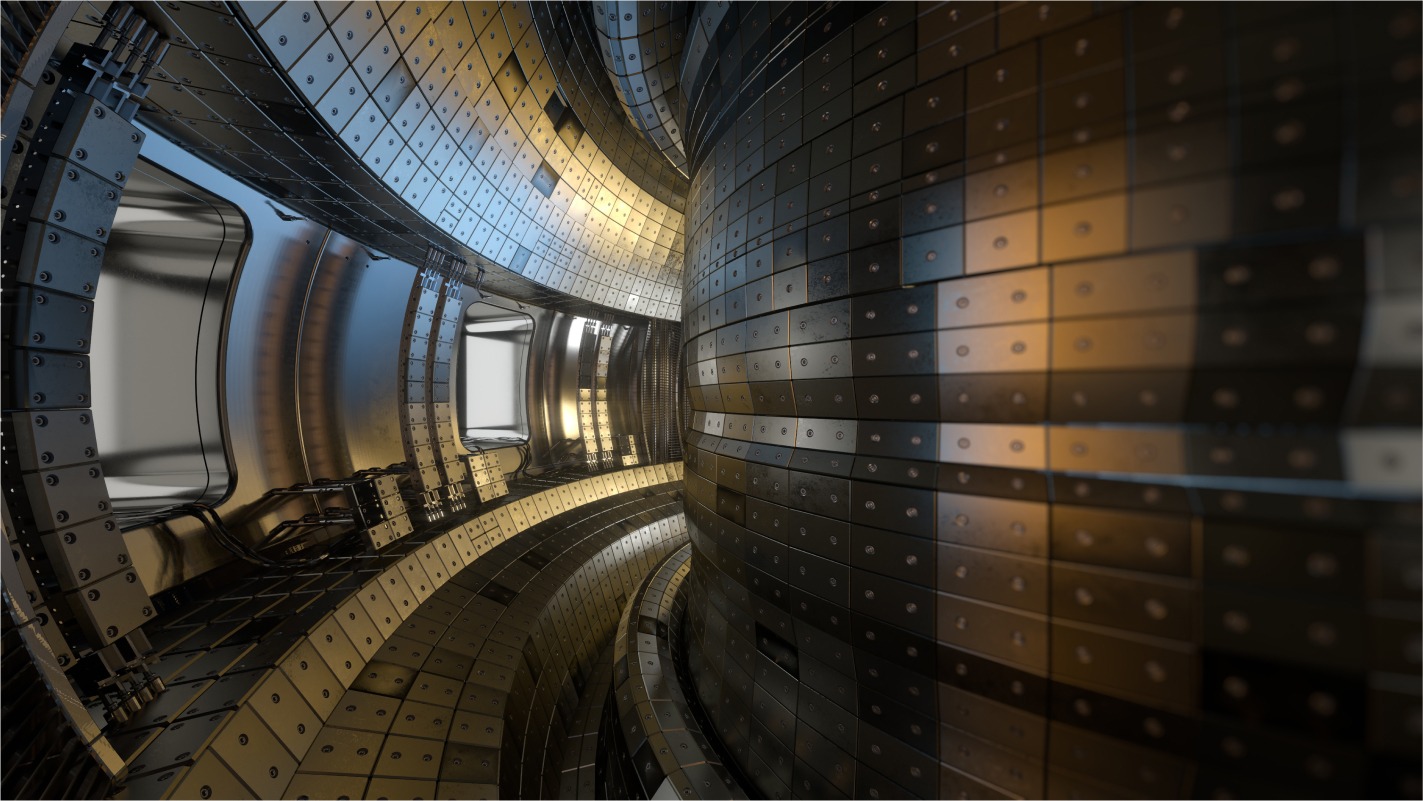
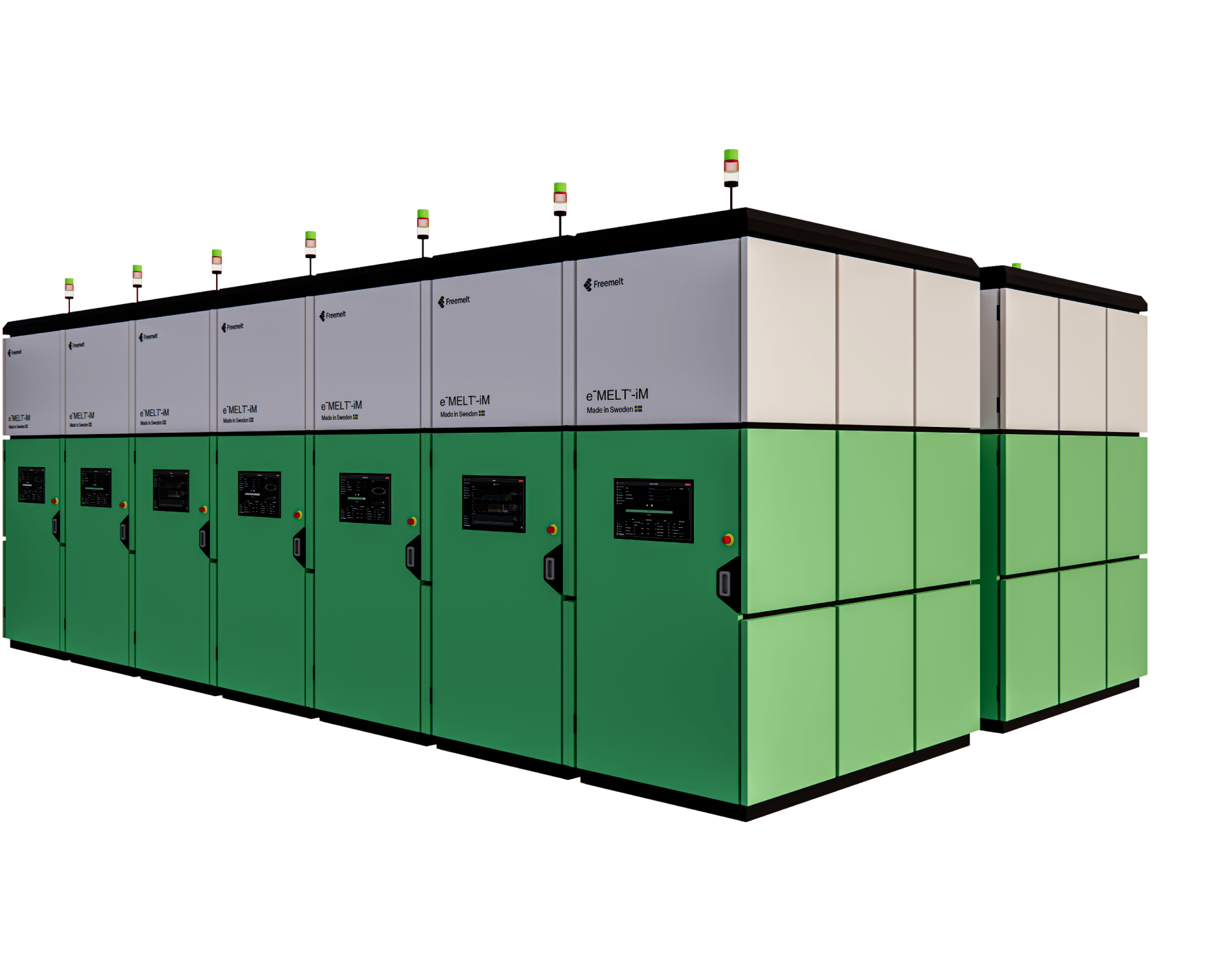
e¯MELT®-iM
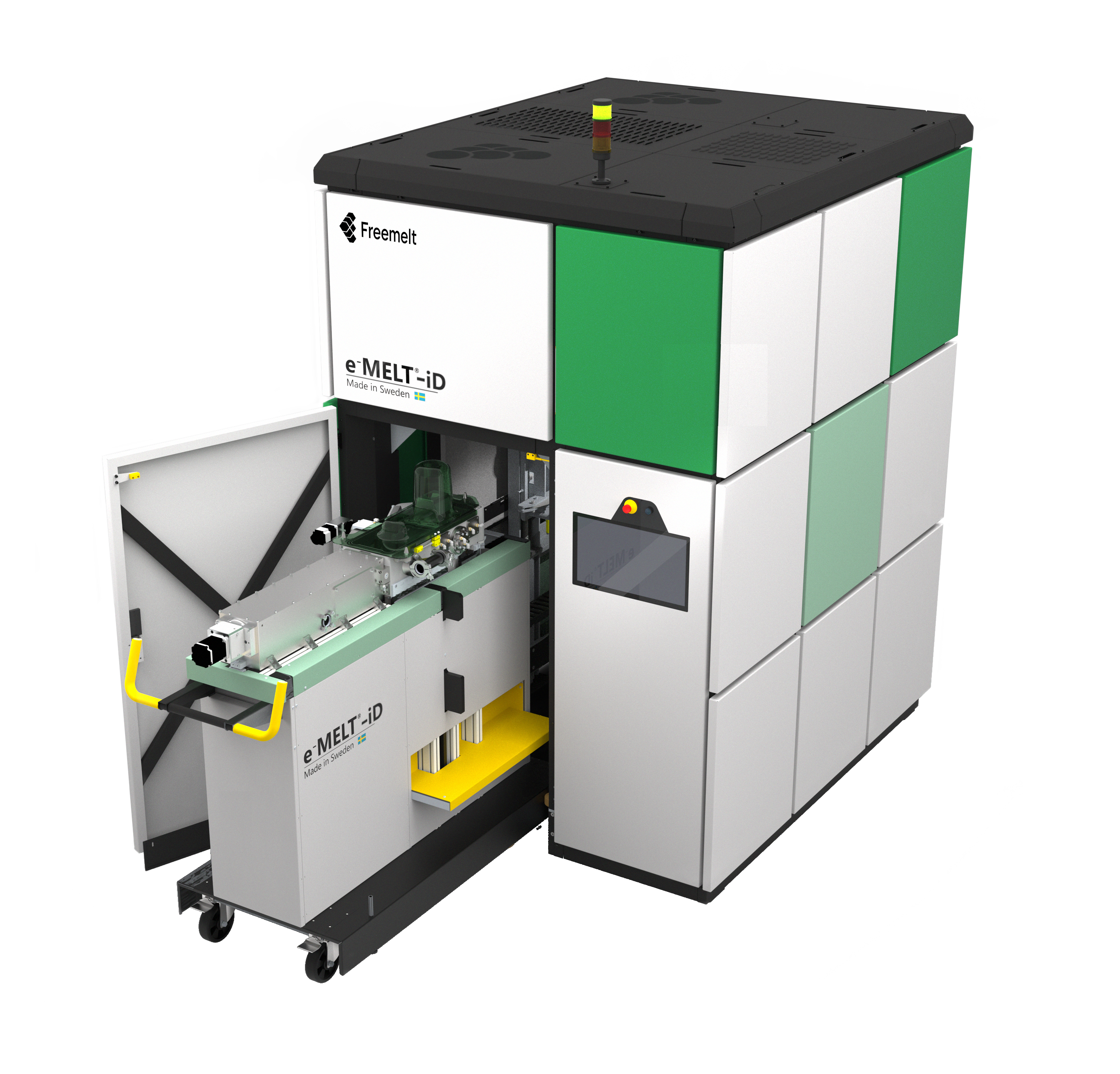
e¯MELT®-iD
Step into the future of metal 3D printing with e¯MELT®-iD. Empower your development work, accelerate your innovation, and redefine the possibilities of additive manufacturing.
Freemelt® ONE
Freemelt® ONE is designed to make materials not yet known to mankind. Materials that engineers dream about. Materials that give us lighter, stronger and more efficient products.
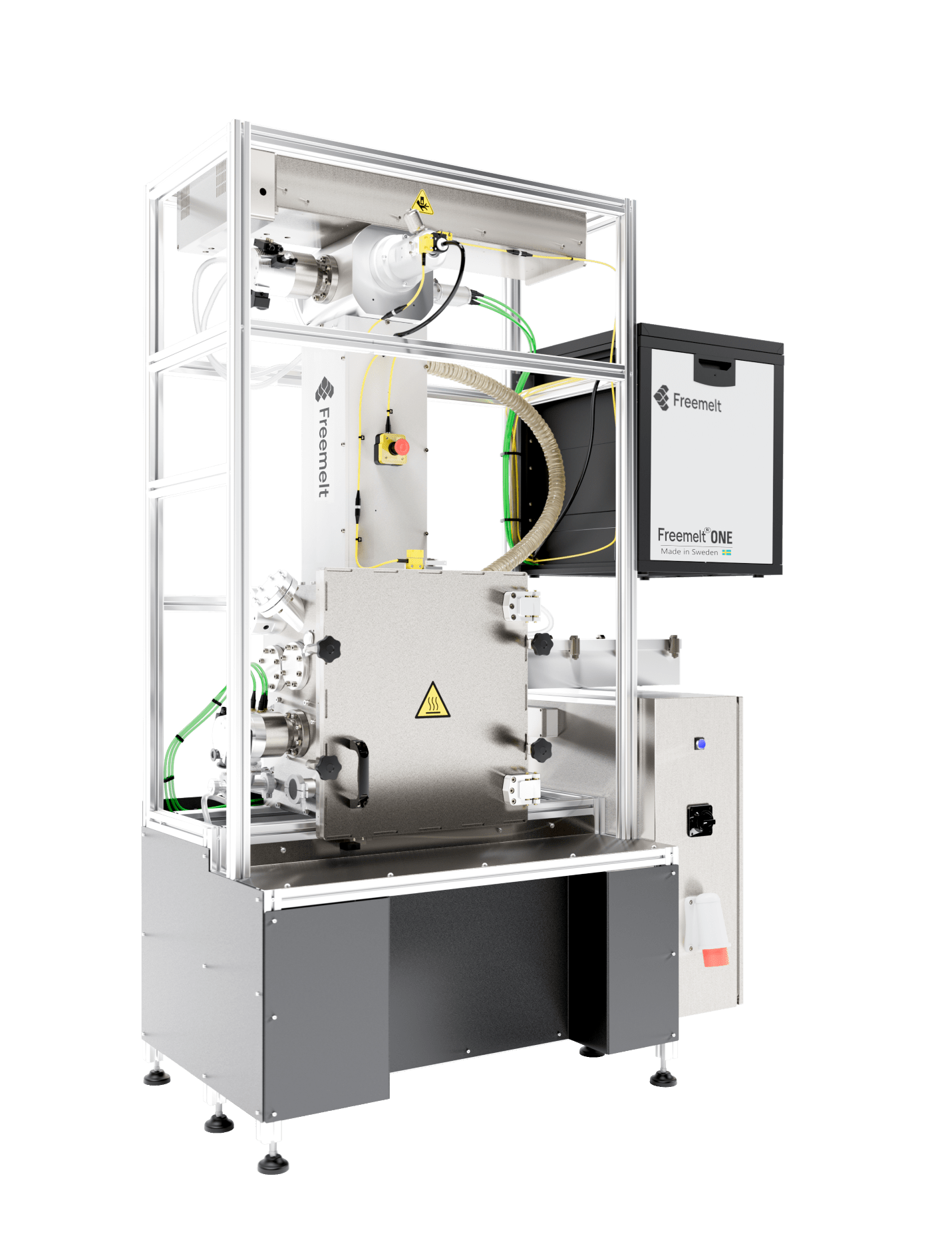
Collaborate with us
Freemelt offers a complete product portfolio supporting you from early material and process development through application development, into a seamless transition to serial production within industries such as medtech, orthopedic implants, energy, defense, and beyond.
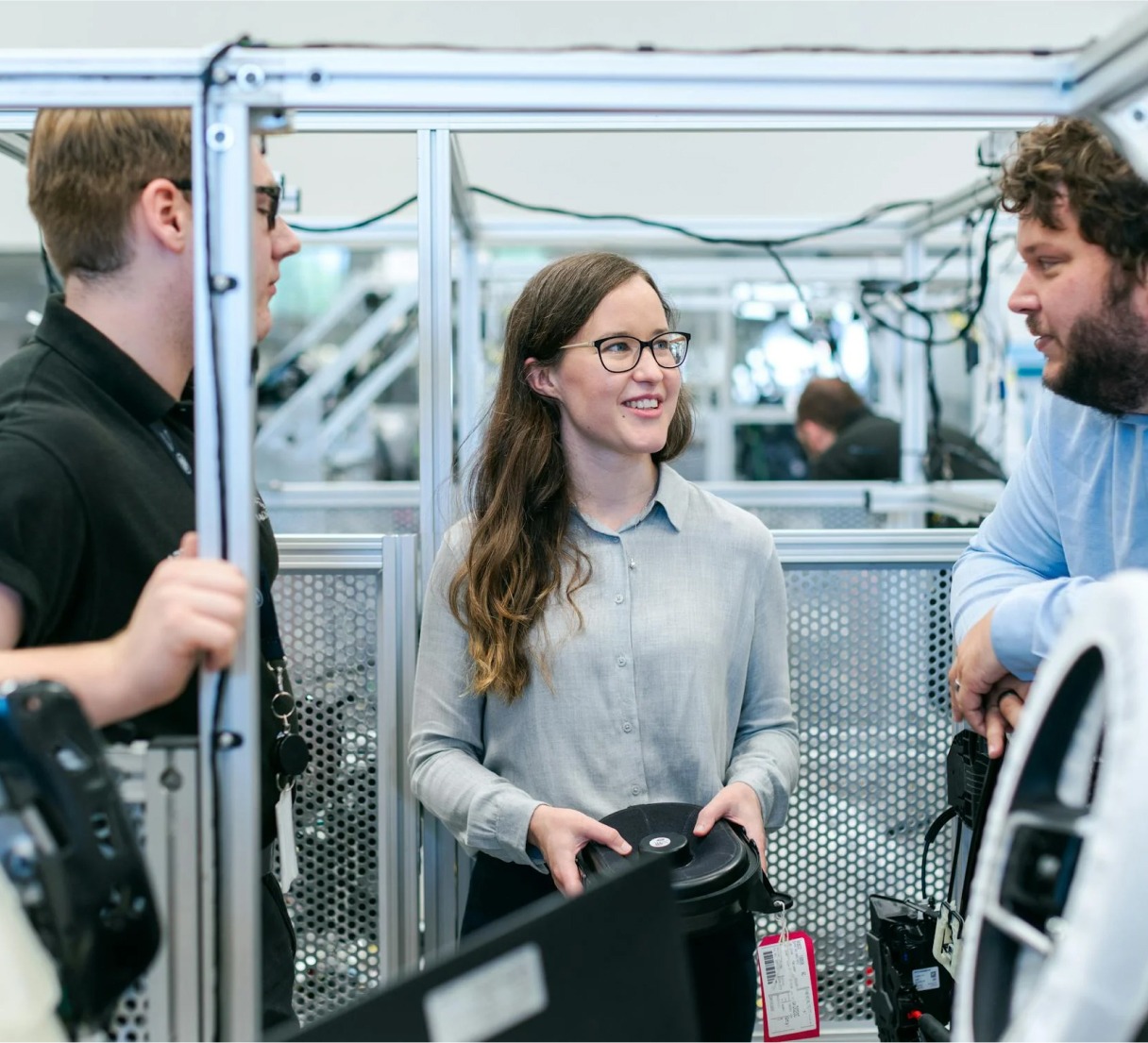
Titanium alloy (Ti-6Al-4V)
Titanium alloy is a key material in orthopedic implants due to its strength, lightness, biocompatibility, and corrosion resistance. Freemelt’s E-PBF technology enhances titanium implant production by enabling complex geometries like solid cores with porous surfaces, and efficient stacking to boost productivity.
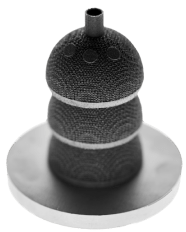
Pure tungsten
Tungsten’s heat resistance and density are vital for Fusion Energy, Defense, and medical X-ray equipment. Freemelt’s E-PBF technology overcomes the challenges of tungsten’s high melting point and brittleness, producing dense, crack-free parts with minimal oxygen uptake, opening new possibilities.
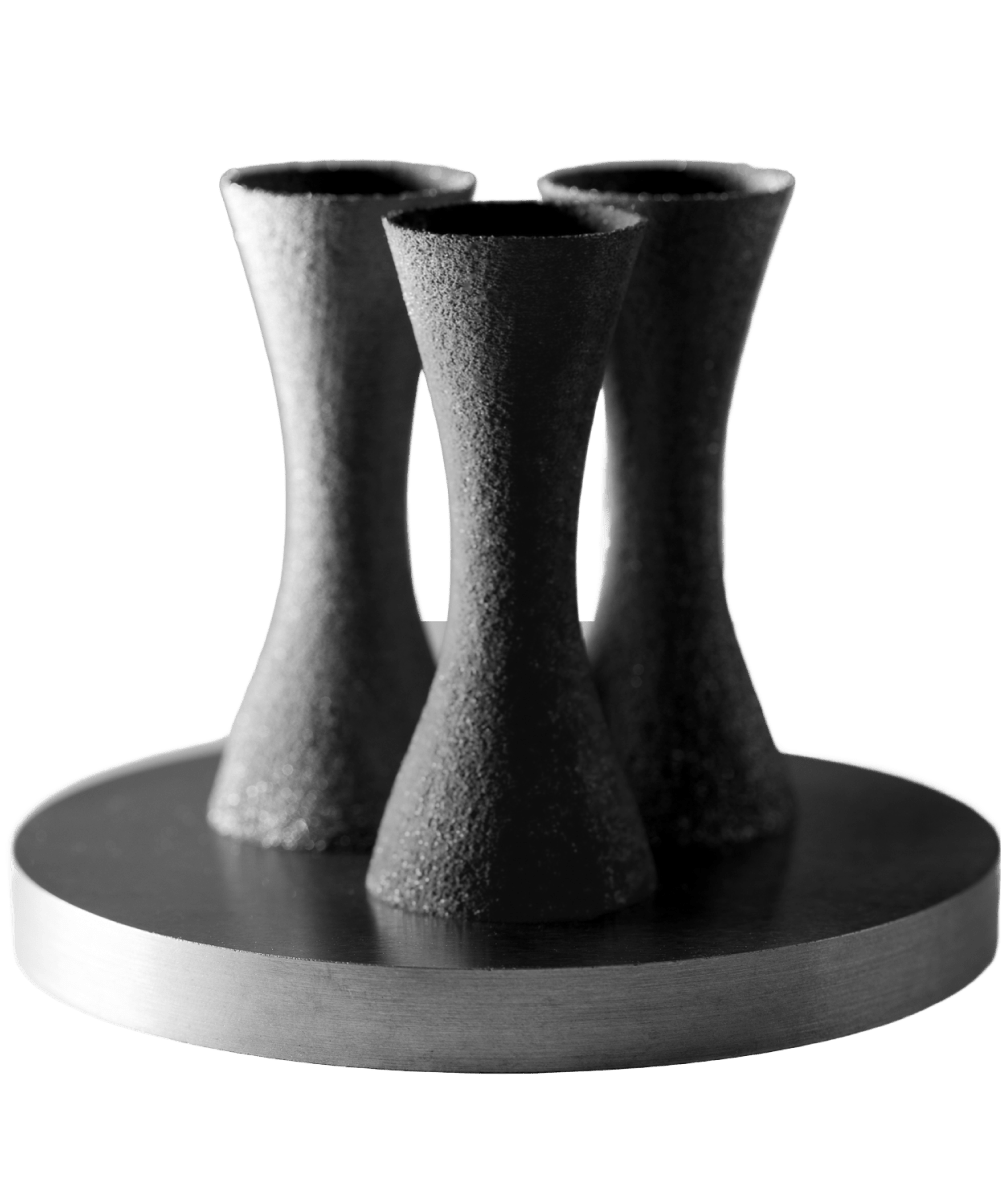
High-purity copper
Copper’s conductivity is essential for advanced heat and electrical systems, particularly in electric vehicles. Freemelt’s E-PBF technology excels where traditional 3D printing falls short, optimizing copper’s microstructure for electromagnetic applications through superior vacuum quality and spot melting technology.
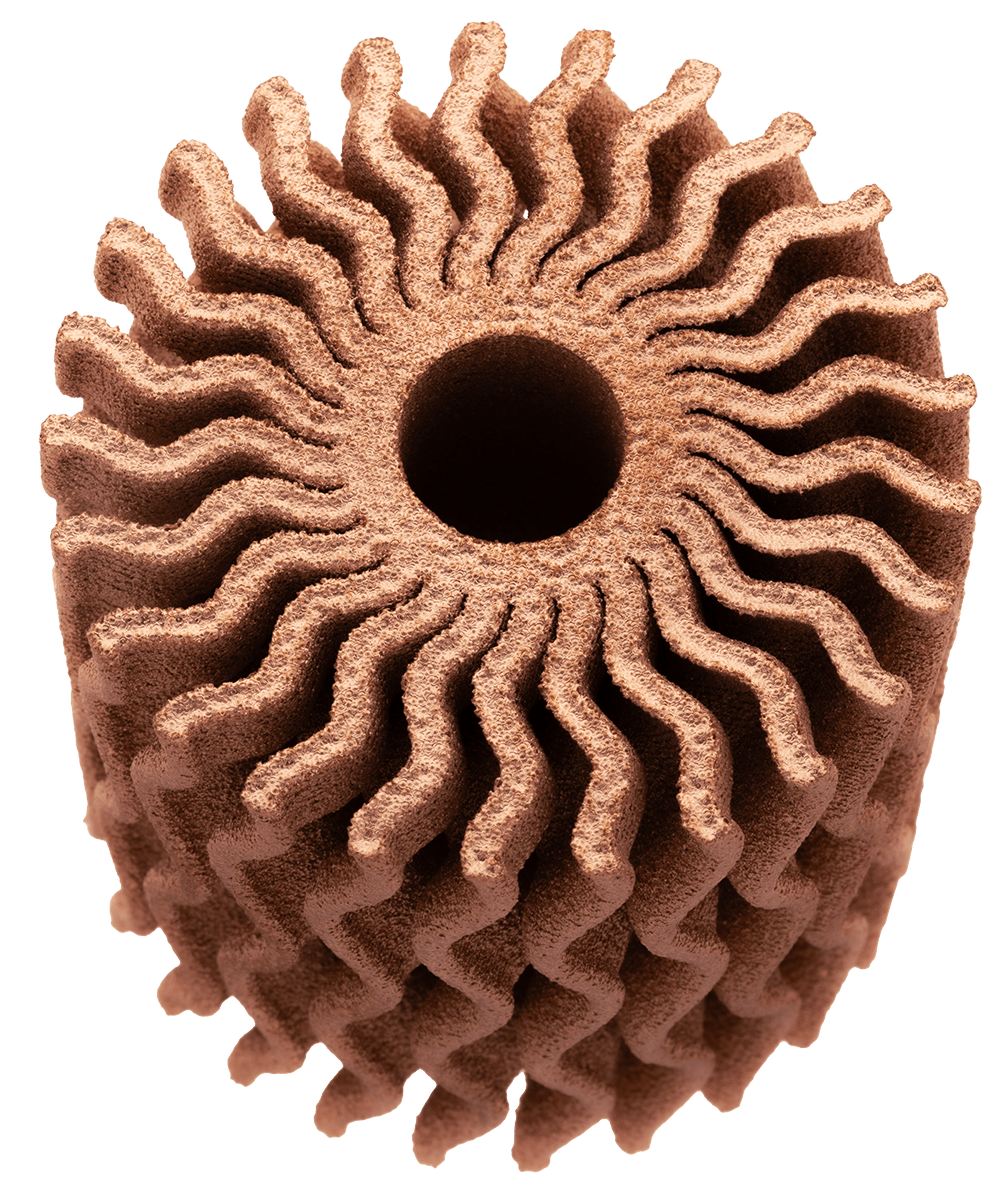
Latest from Freemelt
Freemelt receives order for Freemelt ONE from the University of Toronto
Freemelt has received an order from the University of Toronto for the delivery of a Freemelt ONE machine. The order is strategically important, marking Freemelt’s first machi…
Freemelt receives order for Freemelt ONE from a German industrial company
Freemelt has signed an agreement with a leading global industrial company based in Germany to rent a Freemelt ONE machine. This marks the first delivery of a Freemelt ONE to an ind…
Freemelt receives order for Freemelt ONE from the Swedish defense industry
Freemelt has received an order from a customer within the Swedish defense industry for the research machine Freemelt ONE. The machine will be used in materials research and develop…
Freemelt receives order for Freemelt ONE from NC State University
Freemelt has received an additional order from the Center for Additive Manufacturing and Logistics (CAMAL) at North Carolina State University (NC State University) for the Freemelt…
Key personnel subscribe to options and qualified employee stock options
Following the decision at the general meeting on May 21, 2025, Freemelt has established a long-term incentive program by issuing so-called qualified employee stock options (“…