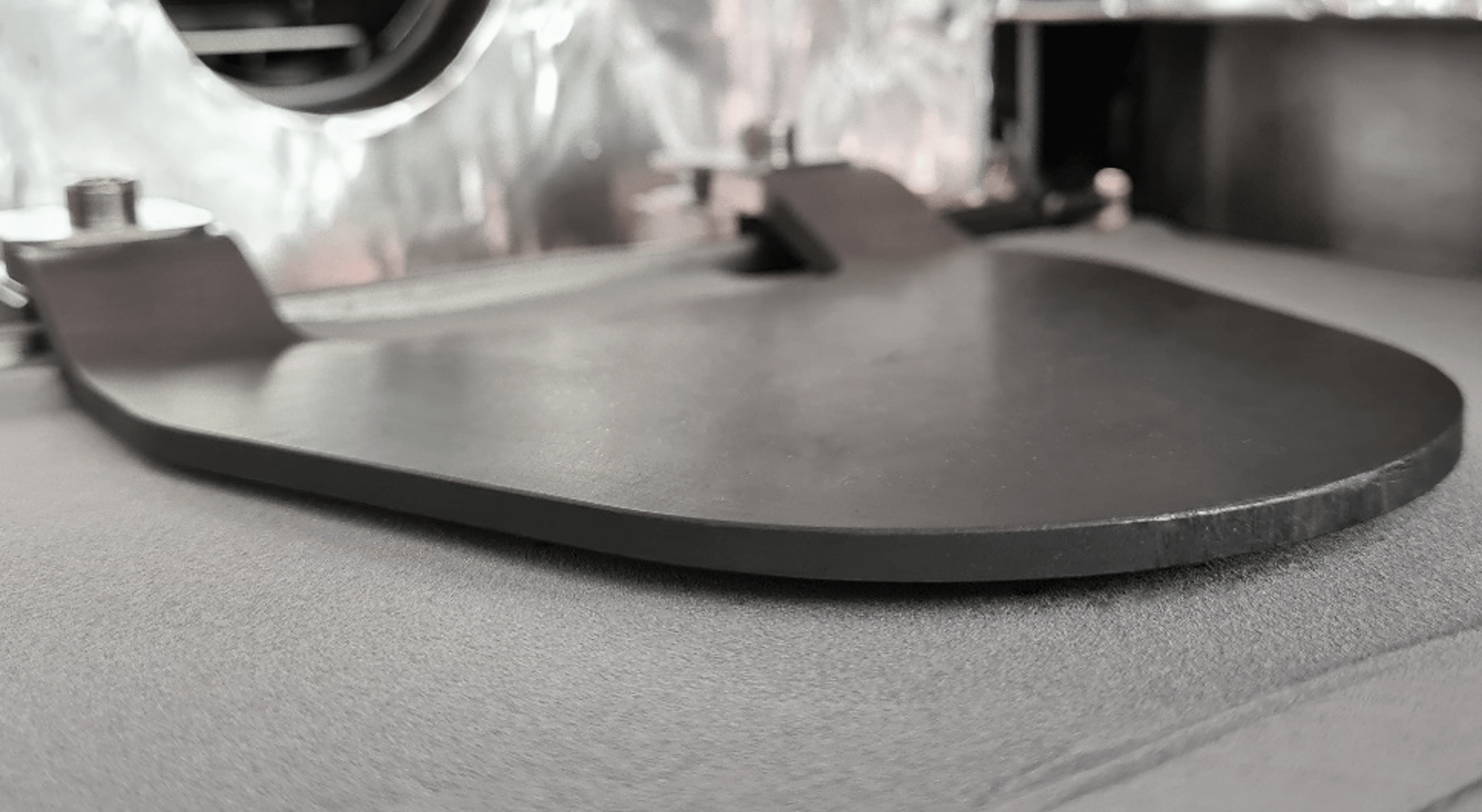
ProHeat® – our unique solution for smoke-safe EBM processing
Problem ‐ Smoke
Scattering of particles, also known as ”smoke,” may pose a challenge for certain powder materials with Electron Beam Melting (EBM). This phenomenon may occur if the electron beam adds too much electric charge the powder bed, leading to Coulomb repulsion. As a result, the powder drifts away from the bed, resembling smoke:
Smoke evolution in a powder bed. Photo courtesy of Prof. M. Zäh, Technical Univ. Munich. Shown with permission.
Different materials and particle shapes exhibit varying degrees of susceptibility to smoke. Spherical powders of titanium alloys, such as Ti‐6Al‐4V, are particularly prone to smoke. This is because these alloys inherently have a thin, insulating oxide layer on the particles’ surface. Consequently, the charge from the electron beam may dissipate too slowly, and the accumulated charge can be strong enough to repel the particles. For any given material, fine powders are generally more smoke‐sensitive than coarse powders, as the surface‐to‐volume ratio is higher. A spherical powder is also more smoke-sensitive than an irregular one, due to differences in powder friction. Irregular particles lock each other in the powder bed.
Solution ‐ Preheating and ProHeat®
To mitigate smoke during the build process, the conventional approach is to preheat the powder before melting, by scanning an electron beam rapidly over the powder bed in specific patterns. This preheating causes light sintering and improved electrical conduction. However, some powders are too smoke‐sensitive to be preheated directly by the beam. ProHeat® is a patented solution that addresses this issue. It involves placing a conductive plate between the powder bed and the electron beam
Operating principle of ProHeat®
ProHeat® functions by lowering the plate closely above the powder bed and heating it red hot using the electron beam. The plate is grounded, preventing it acquiring a charge during this process. The high heat conductivity of the plate allows for a precise preheating of the powder without interaction with the electron beam.
Additionally, the conventional solution to the smoke problem also involves insertion of inert gas into the vacuum to help dissipate electric charge. ProHeat® eliminates this need for expensive high‐purity gas such as helium or argon.
CAD model of the ProHeat® plate as installed in Freemelt ONE
The choice of graphite
We have chosen graphite as the material for the ProHeat® plate. Graphite is commonly used in vacuum furnaces due to its unique properties at high temperature.
Graphite retains high strength above 2000 degrees C and has excellent resistance to thermal cycling. It does not bend or break with heavy use. Furthermore, the lightness of the carbon atom minimizes energy loss due to backscattering of the electrons, optimizing the efficiency of the heating process. A plate in metal would exhibit higher energy loss.
The low density of graphite is also beneficial for mechanical reasons. A graphite plate is easy to lift and move quickly in a vacuum chamber.
Powder life cycle extension and easier post-processing
It is known that a hot powder bed is prone to pick up oxygen from residual moisture in the vacuum chamber. In contrast to conventional preheating, ProHeat® has the capability of preheating very small powder bed areas, leaving a larger powder area unsintered. This opens up for a lower oxygen pickup in the powder, extending the powder lifetime and saving money for the user.
An additional benefit of reduced sintering area is that the sintered powder cake surrounding finished builds will be smaller. This saves post-processing time.
Advantages of ProHeat®
ProHeat® offers an innovative and elegant patented solution to the problem of smoke. By preheating the powder bed with infrared radiation rather than the electron beam, the build process is configurable and cost effective. The fear of smoke events is gone, even for fine powders and smoke-sensitive alloys.
In conclusion, ProHeat® offer several advantages:
- ProHeat® significantly speeds up the development of new materials. By eliminating concerns about smoke‐related issues and failed builds, engineers and researchers can focus on innovation and the continuous improvement of their designs. Time-consuming experimentation with preheating parameters is no longer needed.
- ProHeat® opens up for successful EBM processing of materials that were previously considered impossible due to extreme smoke sensitivity.
- ProHeat® facilitates faster post-processing after the build is complete and opens up for extended powder reuse and less material waste.
- ProHeat® eliminates the need of expensive helium gas for smoke prevention. Helium is a scarce, non-renewable resource on earth.
With ProHeat®, users can fully leverage the potential of EBM while fostering efficiency, sustainability, and cost‐effectiveness.
Read more about Freemelt ONE.
2023-08-17 12:32:24