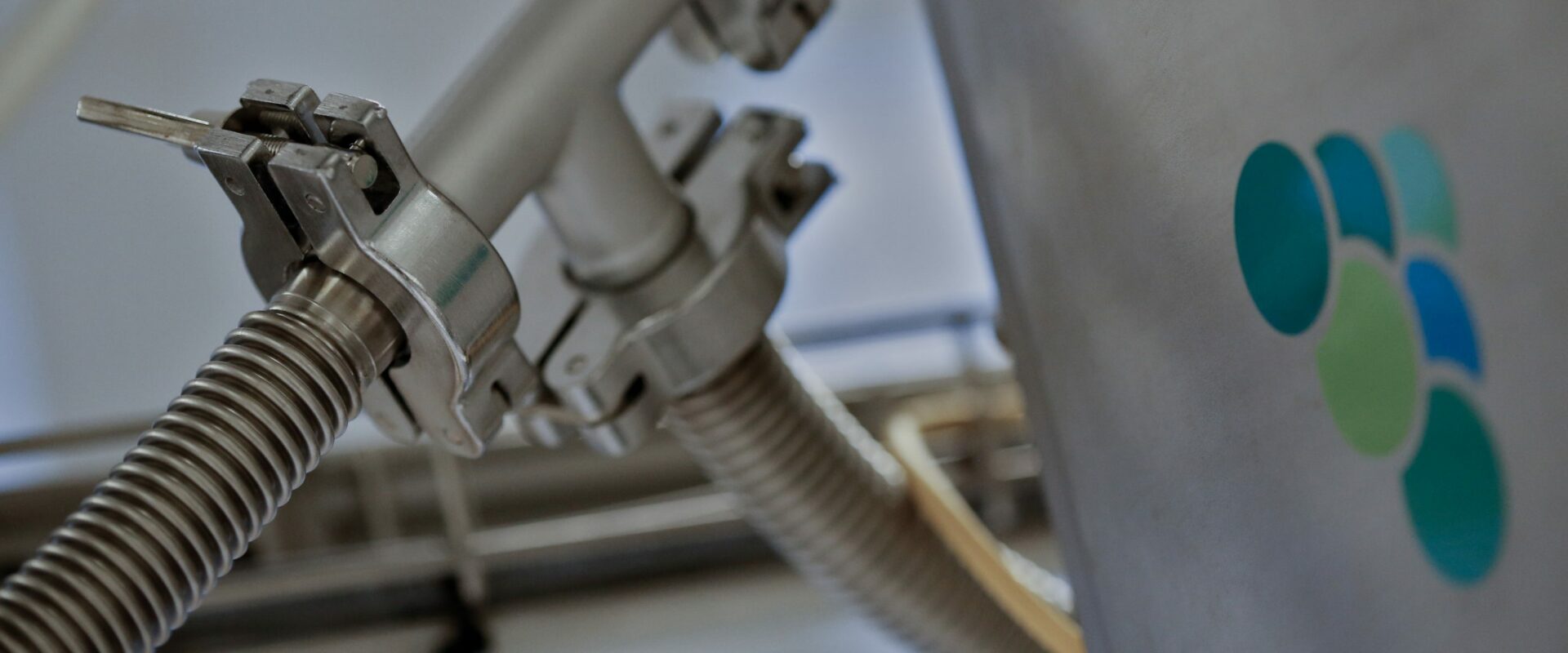
What gives the cleanest environment – inert gas or high vacuum?
There are many processes that must be carried out in absence of air, due to the fact that air exposure contaminates or spoils the process. One such example is hot metalworking of reactive metals, e.g. casting or welding, where a chemical reaction with oxygen or nitrogen would be detrimental to material properties. Another example is additive manufacturing of metal components by powder bed fusion.
In order to protect a process from air exposure, one usually has two options:
- The process chamber can be flushed with argon gas or another inert gas of sufficient purity. The inert gas is in most cases kept at near atmospheric pressure.
- The process chamber can be pumped down to a vacuum of a sufficient quality.
Both alternatives may be good enough for protecting your process, but which one is the best if cleanliness is your top priority? I will try to figure that out.
Inert gas
An inert gas is a gas that is unreactive in its environment. The noble gases (helium, neon, argon, krypton, xenon, and radon) are considered inert in most applications. Argon is the cheapest noble gas and thus the most frequently used. In applications insensitive to chemical reactions with nitrogen, even nitrogen gas (N2) may be used as inert gas.
When speaking about inert gas, it is common to specify the contamination level in ppm, parts-per-million. A contamination level of 100 ppm, for example, means that in a random sample of 1 million molecules of the inert gas, you will find 100 foreign molecules. It is important to understand that parts-per-million is a relative measure which must be converted to an absolute measure to be useful.
The true impact of a contaminant is determined by the partial pressure of the contaminant. Partial pressure can be measured in Pascal, millibar, Torr or whatever pressure unit you prefer. The partial pressure is the absolute measure we need to compare purity of inert gas versus purity of vacuum. For an inert gas at atmospheric pressure, 1 ppm corresponds to a partial pressure of 0.001 mbar (SI unit lovers may note that 1 mbar = 100 pascal).
Inert gases are commercially available at various purity levels, and of course, the gas cost increases with purity level. Argon gas is typically available in qualities such as indicated in Table 1 below.
Some suppliers might be able to offer argon gas even somewhat below 1 ppm contamination level. However, rest assured that it will be very, very expensive.
Vacuum
In its widest definition, a “vacuum” is a gas volume at any pressure below atmospheric pressure. A more scientific approach is to define various vacuum levels according to the residual gas pressure inside a vacuum vessel, as shown in Table 2 below.
What gives the cleanest environment in a process chamber? Inert gas or high vacuum?
The answer is given by the figures in Table 1 and Table 2.
For a process chamber carefully flushed with an ultrahigh-purity inert gas at atmospheric pressure, you could approach an impurity partial pressure of 0.001 mbar, at least in theory. In practice, you may end up at 0.01 mbar or 0.1 mbar, due to impurity gas trapped in your process, or leaks, or for the reason of high cost of inert gas.
For an evacuated process chamber, you can routinely reach a residual pressure below 0.0001 mbar if you allow an hour for pumping.
Conclusion
High vacuum is the way to go if cleanliness is your top priority. For all practical purposes, high vacuum is at least ten times cleaner that inert gas atmosphere. In most cases, high vacuum is 100x cleaner, or even 1000x cleaner than inert gas. Sometimes even 10000x cleaner.
2020-02-13 05:41:20
Author: Ulf Ackelid, Principal Scientist, founder Freemelt AB