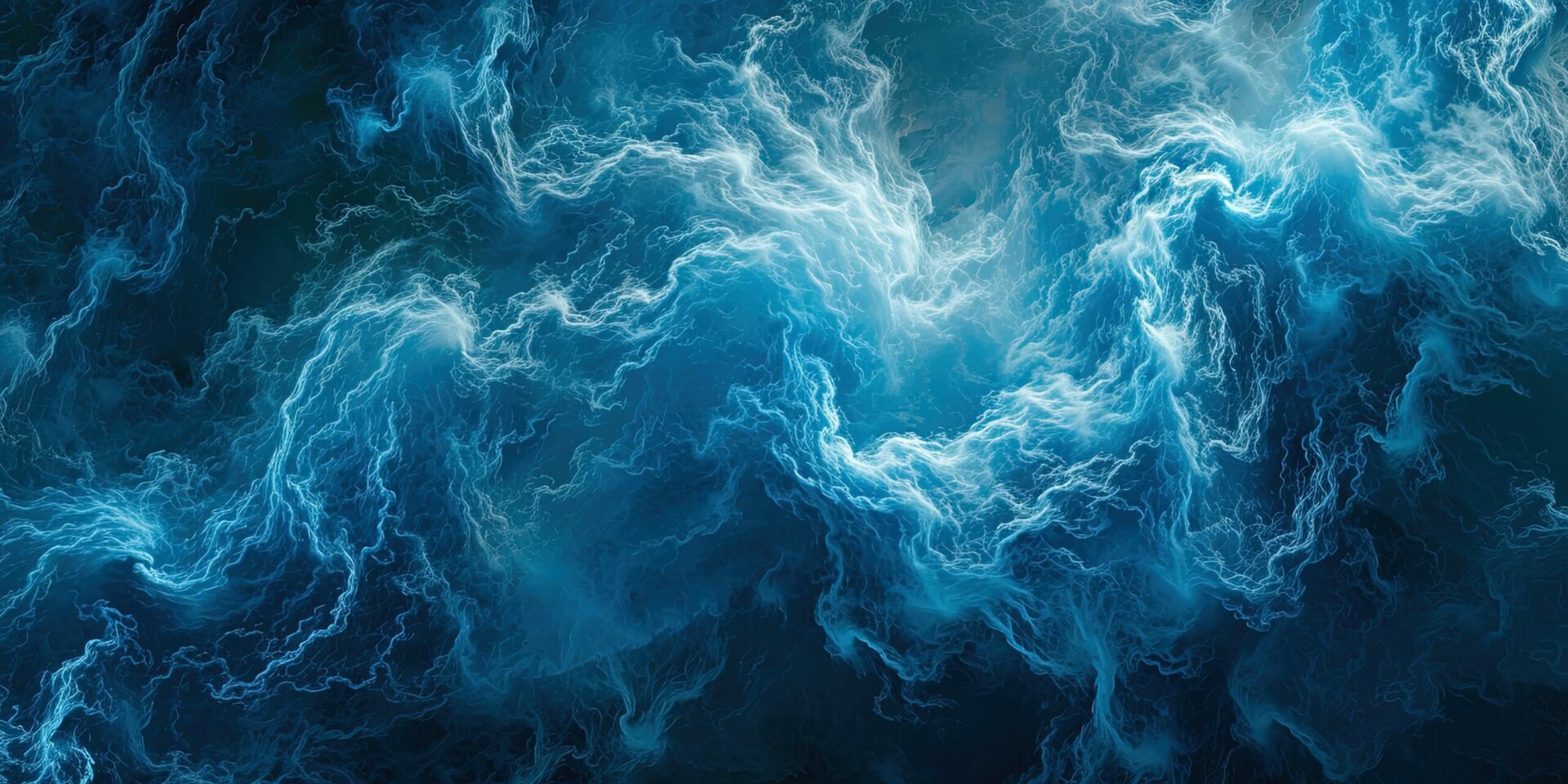
E-PBF Myth #3 “E-PBF manufacturing requires several hours of cooling”
This is the third publication in a series of short articles where we address common myths about E-PBF. We elaborate on how, and why the myths have arisen and how Freemelt’s technology and products overcome the myths.
Today we dive into myth #3: Several hours of cooling needed
One common statement about E-PBF is that it requires several hours of cooling between the build jobs, which results in reduced productivity. This belief is related to that E-PBF compared to L-PBF (Laser Powder Bed Fusion) technology is a hot process in a vacuum requiring cooling between the build jobs. Most of the E-PBF systems available on the market don’t have an efficient cooling mechanism built into the machine, resulting in several hours of post-cooling between build jobs, high machine-down time, and loss in productivity. This perception of prolonged cooling times post-build has in many cases “disqualified” E-PBF as manufacturing technology.
Freemelt’s unique machine design enables post-cooling in less than one hour!
Freemelt is redefining the E-PBF industry with its unique machine design. One of the unique features of our industrial system e–MELT® is the active cooling mechanism where we use a system based on a water-jacketed build tank, reducing post-build cooling significantly to less than an hour, enabling faster turnaround times and increased productivity.
This makes e–MELT® highly suitable for the production of demanding materials such as tungsten, where the active cooling mechanism enables the production of dense and crack-free tungsten parts. Tungsten as a material has high mechanical strength, high corrosion resistance, and the highest melting point of all elements, which makes it suitable for use in industrial processes involving extreme temperatures, such as fusion energy production. However, due to its extreme melting temperature, tungsten is difficult to manufacture with traditional methods which makes additive manufacturing particularly attractive for tungsten fabrication. An additional benefit of the cooled build tank is that seals are at a much lower temperature allowing better seal arrangements.
Illustration 1:
Photo taken at the end of a build in e–MELT®, showing process temperature of 1057o C (on the right side where the arrow is)
Illustration 2:
Photo taken 30 min after end of a build in e–MELT®. In only 30 min the temperature went down from process temperature of 1057o C to 90oC (below 100 oC that is the allowed temperature to open the machine).
Freemelt’s unique E-PBF technology and products
With Freemelt’s technology, E-PBF becomes more versatile, allowing for intricate designs and complex geometries with the potential to revolutionize industries including medical equipment, energy, aerospace, defense, and orthopedic implants.
Within these segments, Freemelt aims to be perceived as a productivity partner, providing value throughout the entire product lifecycle by generating increased productivity, reducing operating costs, and maximizing long-term customer value.
Read more:
eMELT-iM: The Industrial 3D printer for mass production
Electron beam powder bed fusion processing of pure tungsten
E-PBF Myth #1 “E-PBF manufacturing requires coarse powder”
E-PBF Myth #2 “E-PBF manufacturing requires spherical powder”
Freemelt’s materials strategy: Powering large-scale 3D metal printing
Nine myths about Electron Beam Powder Bed Fusion
2024-06-25 10:15:37