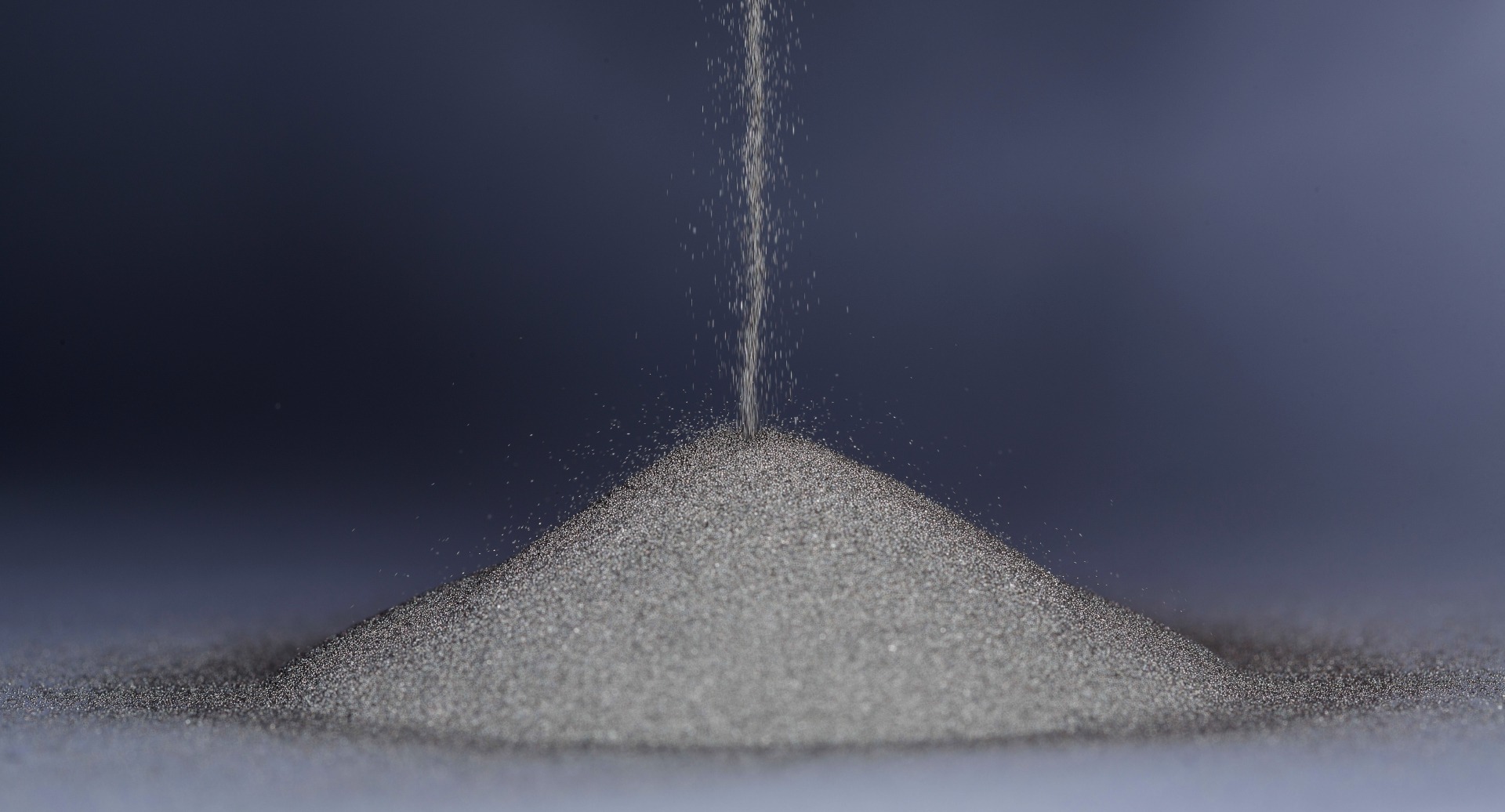
Rediscovering Titanium: New ways to make old things
One of the first successfully processed alloys by Electron Beam Powder Bed Fusion (EB-PBF) was Ti-6Al-4V around 20 years ago. Also known as Titanium grade 5, or simply just as Ti64, this material offers high strength to weight ratio, high corrosion resistance and good biocompatibility. Given these set of properties it is not surprising that it has become the material of choice for applications within the aerospace and the orthopedic implant industries [1]. Ti-6Al-4V ELI (Extra Low Interstitials), or Titanium grade 23, is preferred for the latter since it has a lower oxygen content than grade 5.
But why additive manufacturing (AM) and why EB-PBF? What is the added value that this technology offers that can upset the conventional ways of manufacturing? Here is a short list of the benefits of using EB-PBF to process Ti64:
1. High temperature processing: Residual stress and cracking because of large thermal gradients make a lot of alloys not weldable at room temperature. Ti64 is processed at around 600° to ensure proper fusion between layers. The finished part is free of internal stress and has also undergone an in-situ annealing process meaning that there are little to no martensitic phases in the microstructure left.
2. High purity chamber: EB-PBF operates at high vacuum chamber in the order of 10-5 bar. Titanium is an element that likes oxygen. Processing Ti64 at high temperatures without vacuum would make it react with oxygen by not only generating a thick oxide layer but also by generating an undesired case of alpha-phase on the surface of the part making it brittle and prone to crack initiation.
3. Part customization and complexity for free: With the design freedom of additive manufacturing, it is easier than ever to make custom parts with complex designs that otherwise could be either impossible or very expensive to make via a casting or forging process. Conventional manufacturing technologies are great at producing standardized parts on a large scale. However, every design change on a part comes with the need of manufacturing new tooling which has a strong negative effect on the cost.
4. Stacking capabilities: EB-PBF allows for the stacking of parts in the build chamber thanks to the sintered nature of the powder bed. The powder itself acts as a support structure that keeps the parts in place without the need for printing additional supports that would otherwise increase layer times, material waste and post processing time. This makes it possible to optimize the volume usage of the build chamber in an EB-PBF system.
Freemelt has not only has developed its own range of EB-PBF systems (ranging from research-oriented to mass-production), but also, its own process parameters for Ti64 using its own developed spot melting software Pixelmelt®.
Spot melting is a game changer in EB-PBF. Instead of using the conventional raster strategy, the electron beam dwells on a specific coordinate for a specific amount of time to melt the powder. Then it jumps to another location to repeat the process.
![]() |
![]() |
Figure 1. Lattice structure printed in Ti-6Al-4V using Pixelmelt®. Strut size is ~450 μm.
The development of new scan strategies based on spot melting opens a new window of opportunities for the development of the Ti64 printing process. Better microstructure control, improved surface quality, removal of support structures, mitigation of gas porosity [2], and fast melt times due to the constant spot size quality of the Freemelt systems are some of the advantages that will bring the quality of AM components to the next level.
![]() |
![]() |
Figure 2. Bright field microstructure comparison of two EB-PBF manufactured samples with gas atomized powder. The left sample was printed with the conventional line scan and the right sample was printed with spot melting. The spot melted sample has smaller and fewer gas pores.
Learn more about Pixelmelt® and Freemelt® ONE.
References:
[1] Nguyen H, Pramanik A, Basak AK, Dong Y, Prakash C, et al. A Critical Review on Additive Manufacturing of Ti-6Al-4V Alloy: Microstructure and mechanical properties. Journal of Materials Research and Technology 2022. https://doi.org/10.1016/j.jmrt.2022.04.055
[2] Nandwana P, Lee Y. Influence of Scan Strategy on Porosity and Microstructure of Ti-6Al-4v Fabricated by Electron Beam Powder Bed Fusion. Materials Today Communications 2020. https://doi.org/10.1016/j.mtcomm.2020.100962.
2024-04-11 09:36:54