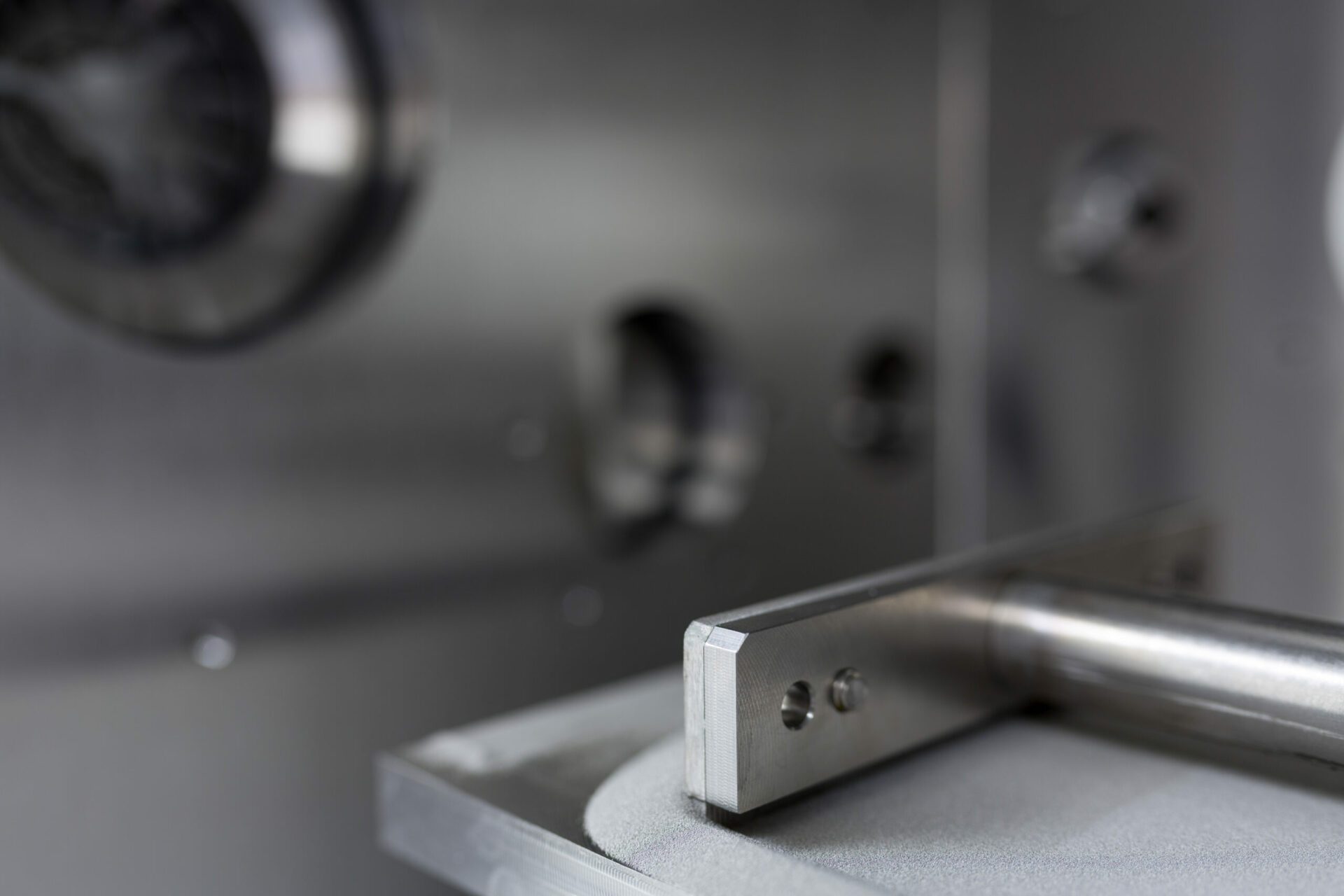
E-PBF Myth #4 “E-PBF manufacturing is limited to columnar microstructure”
This is the fourth publication in a series of short articles where we address common myths about E-PBF (Electron Beam Powder Bed Fusion). We elaborate on how, and why the myths have arisen and how Freemelt’s technology and products overcome the myths.
Today we will dive into myth #4 “E-PBF manufacturing is limited to columnar microstructure”
Columnar microstructures are a consequence of the melting strategy employed and the ensuing thermal conditions that affect the columnar-equiaxed transition for a given material. The most commonly used melting strategy in E-PBF is line melting with a ”hatching” strategy. This strategy in combination with high process temperature in E-PBF processing promotes ”epitaxial growth” that often leads to a columnar microstructure. Columnar microstructures are not inherently bad. It has benefits such as better creep strength along the columnar direction, which is taken advantage of in demanding applications such as turbine blades in gas turbine engines. However, if an application requires an equiaxed microstructure, it is possible to achieve that in the E-PBF processing by employing innovative scan strategies for melting.
Pixelmelt® – Freemelt’s innovative spot melting technology enables the production of non-columnar microstructures!
It has been demonstrated that it is possible to generate equiaxed microstructure with E-PBF processing for materials such as Alloy 718, Alloy 247, and pure tungsten, etc. With Freemelt’s open-source philosophy, researchers can develop innovative scanning strategies to tailor microstructure in components to suit the requirements. Freemelt has developed Pixelmelt®, a unique spot melting technology, where each powder layer is melted in discrete spots, “pixel-by-pixel”, rather than in continuous lines. Pixelmelt® is more than just software, it’s a catalyst for innovation, offering a myriad of benefits that will redefine the way you tailor your material properties.
Freemelt’s unique E-PBF technology and products
With Freemelt’s technology, E-PBF becomes more versatile, allowing for intricate designs and complex geometries with the potential to revolutionize industries such as Defense, Energy, MedTech, and beyond. Within these segments, Freemelt aims to be perceived as a productivity partner, providing value throughout the entire product lifecycle by generating increased productivity, reducing operating costs, and maximizing long-term customer value.
Read more about spot melting and E-PBF myths
Why melting “Pixels”? | Freemelt
Spot Melting | Freemelt
Design of Experiments in Freemelt ONE | Freemelt
E-PBF Myth#1, ”E-PBF manufacturing requires coarse powder”
E-PBF Myth #2, “E-PBF manufacturing requires spherical powder”
E-PBF Myth #3, “E-PBF manufacturing requires several hours of cooling”
Nine myths about Electron Beam Powder Bed Fusion | Freemelt
2024-08-26 09:19:04