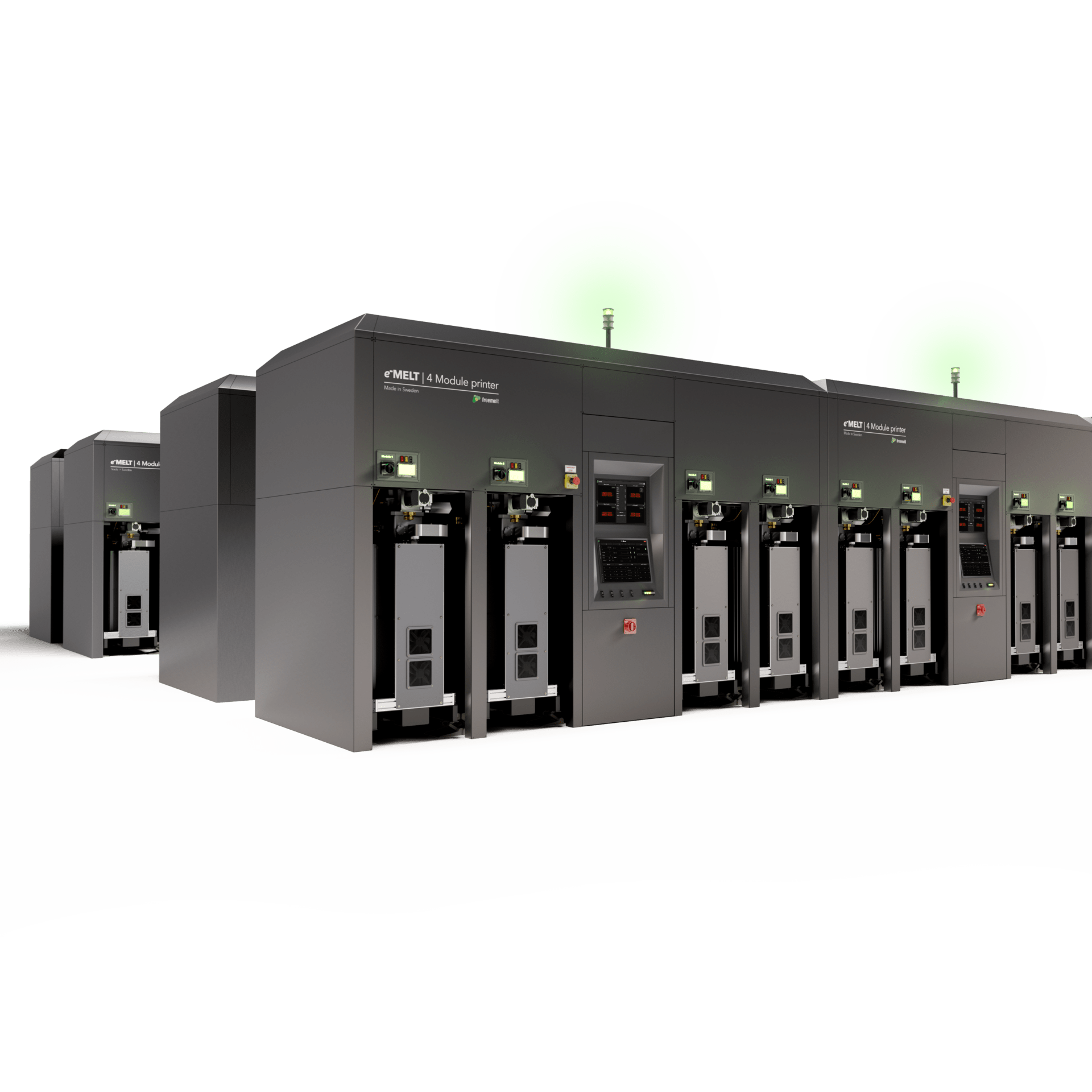
Freemelt’s materials strategy: Powering large-scale 3D metal printing
Freemelt is driven to transform metal additive manufacturing (AM) into a true industrial powerhouse, using our Electron Beam Powder Bed Fusion (E-PBF) technology. Our focus lies in a set of materials carefully selected to maximize the potential of our innovative e–MELT®-iM systems. This combination delivers unmatched productivity and a game-changing part economy in AM. Titanium, tungsten, and copper are our priority materials. Here is why!
Titanium Alloy (Ti-6Al-4V): The implant workhorse
- Huge market opportunity: Titanium is strong, lightweight, biocompatible, and corrosion-resistant – perfect for orthopedic implants. AM is already used for implants to a small extent, and there is a massive growth potential. Freemelt is committed to make AM reach its full capability in titanium implant production.
- Why E-PBF? E-PBF lets us create the special shapes surgeons are dreaming of, such as solid core material combined with a porous surface. Another benefit is the exceptional E-PBF stacking capability, filling up the whole build volume with densely packed implants.
- The Freemelt edge: e–MELT®-iM system sets a new standard for upscaled titanium productivity, achieving the lowest cost per part. Original Freemelt innovations such as ProHeat® and Pixelmelt® pave the way for titanium success.
Pure tungsten: Handling the heat
- Critical applications: Extreme heat resistance, superior radiation shielding, and very high density make tungsten attractive in a variety of advanced technology areas, such as nuclear fusion energy, medical X-ray equipment, and defense applications. However, dense tungsten parts have been difficult or impossible to manufacture in the past, due to its high melting point, brittleness, and poor machinability.
- Why E-PBF? Using high-power E-PBF, the powder bed can be maintained constantly above 1000 degrees C throughout the full build process. At such high temperatures, tungsten is no longer brittle and can be fused into dense, crack-free parts. In addition, since E-PBF is a vacuum process, we can avoid detrimental pickup of oxygen into the tungsten material.
- The Freemelt edge: Our flexible technology, recoater architecture, superior vacuum, and real-time electron detector let us work with various tungsten powder qualities. Low-cost tungsten powders open up new business cases that have previously been unprofitable.
High-purity copper: The conductivity champion
- Market need: Copper’s conductivity makes it essential for advanced heat management and electrical systems. Think electric cars and beyond! Demand is soaring, and manufacturers need cutting-edge production methods.
- Why E-PBF? E-PBF handles the challenge of 3D printing copper, which laser-based systems struggle with. Copper absorbs energy much better from an electron beam. In addition, vacuum is essential to reach the ultra-low oxygen content needed for high-performance conductivity.
- The Freemelt edge: Our superior vacuum quality is key for keeping copper powder more pristine than ever. Combined with our specialized Pixelmelt® processing strategies, it allows us to distribute heat cleverly and tailor copper’s microstructure for advanced electromagnetic applications.
Read more:
e–MELT®-iM
ProHeat®
Pixelmelt®
Rediscovering Titanium: New ways to make old things
2024-05-11 08:27:57